Construction Excellence.
Our Construction Excellence Framework provides innovative approaches to project planning, project management, and project execution to deliver complex construction and infrastructure projects quickly, smartly, and efficiently.

Construction Excellence Framework
-
Selection of a production system suitable for the project according to Lean principles
Develop and coordinate organizational guidelines and work breakdown structure planning
Prepare initial "user agreement" reflecting project goals, requirements, etc., and set final date for no-cost design changes (design freeze).
Preparation of scheduling with budget specifications (L1-L2)
Determine and set up control scheduling
Propose and reconcile change management
Selection of the communication, control and reporting system
-
Monitoring and simplification of the design through the use of standardized modules
Scheduling control of planning and interfaces (according to lean and agile principles)
Coordinate the discussion of the design for each draft submission
Update the user agreement to reflect revisions to the original agreement and new rulings
Execution planning with deadlines, resources, documents, budget (L3-L4).
-
Determination of the award strategy and preparation of the award documents
Monitoring of the purchasing process
Definition of the contract models and design
Monitoring and acceleration of delivery times
-
Development and derivation of the modularization strategy
Selection of the prefabrication partner (national/international)
Overall structuring of prefabrication and control of the production sequence
Monitoring and acceptance of the defined prefabrication scopes
-
Continuous monitoring and control of execution
Project management and control for deadline and cost monitoring (according to the Takt principle)
Integration of the subcontractors into the scheduling
Execution of cycle planning and cycle control with the subcontractors
Control decision and change management
Takt planning and takt control: The origin of a method
More transparency, better coordination and increased productivity: The Takt Planning and Takt Control (TPS) method stands for daily performance management.
Read our blog about the origin of clock planning and clock control
Training as VDI 2553 Lean Construction expert
A holistic approach to the planning and execution of construction projects enables the quality of buildings to be improved and prevents unnecessary consumption of resources. The term "Lean Construction" describes a tried-and-tested approach to the more economical management of construction projects. Lean Construction is thus the adaptation of Lean management, which has long been practiced in the automotive industry, for example, to the construction industry. Together with the VDI, as a certified training partner, we offer a qualification program to become a "Lean-Construction expert according to VDI 2553".
From international experts in the field - with a large number of international example projects from building construction, civil engineering, infrastructure construction and plant construction
Project examples
Increase productivity in planning and construction
In a complex hospital project, the challenge was to efficiently coordinate a multitude of planners and trades while meeting a tight schedule and budget. Involved from construction planning through construction execution, Lean Group implemented a Lean Construction Excellence framework specifically tailored to meet the needs of a project as complex and multi-faceted as a hospital. By applying a phased planning approach and optimizing workflows, productivity was continuously improved during the design and construction execution phases. This enabled the hospital to be completed on schedule and resulted in stable cost compliance.
Rapid construction system shortens execution time for commercial buildings
In a project for the optimization of commercial buildings in the retail sector, Lean Group GmbH developed an innovative rapid construction system in close cooperation with the customer. This system was rolled out throughout Germany after successful concept development. The implementation resulted in a 20% reduction in execution time, which was not only cost effective, but also enabled the client to start business operations faster. This increased profitability and led to higher customer satisfaction. In addition, scaling the solution by rolling it out across Germany enabled further cost savings. Standardization of the construction processes also ensured consistently high quality of the buildings. In addition, the fast-track construction system opened up opportunities for more environmentally friendly construction methods, which reduced the project's environmental footprint.
Innovation project: AI-driven optimization of construction progress and forecasts.
An innovation project investigated the use of artificial intelligence (AI) to optimize construction progress and improve forecast accuracy. By integrating AI algorithms into existing project management tools, a more accurate analysis of construction progress was achieved. This enabled more accurate forecasting of time and resource requirements, which in turn led to more efficient allocation of personnel and materials.
The implementation of AI technology had several benefits. First, it significantly improved the accuracy of project forecasts, enabling better planning and thus cost savings. Second, the AI-driven analysis allowed early identification of bottlenecks and risks so that proactive measures could be taken to avoid delays. Third, the improved data analysis led to increased transparency in the course of the project, which facilitated communication between stakeholders and strengthened trust in project management.
Contact us for more information
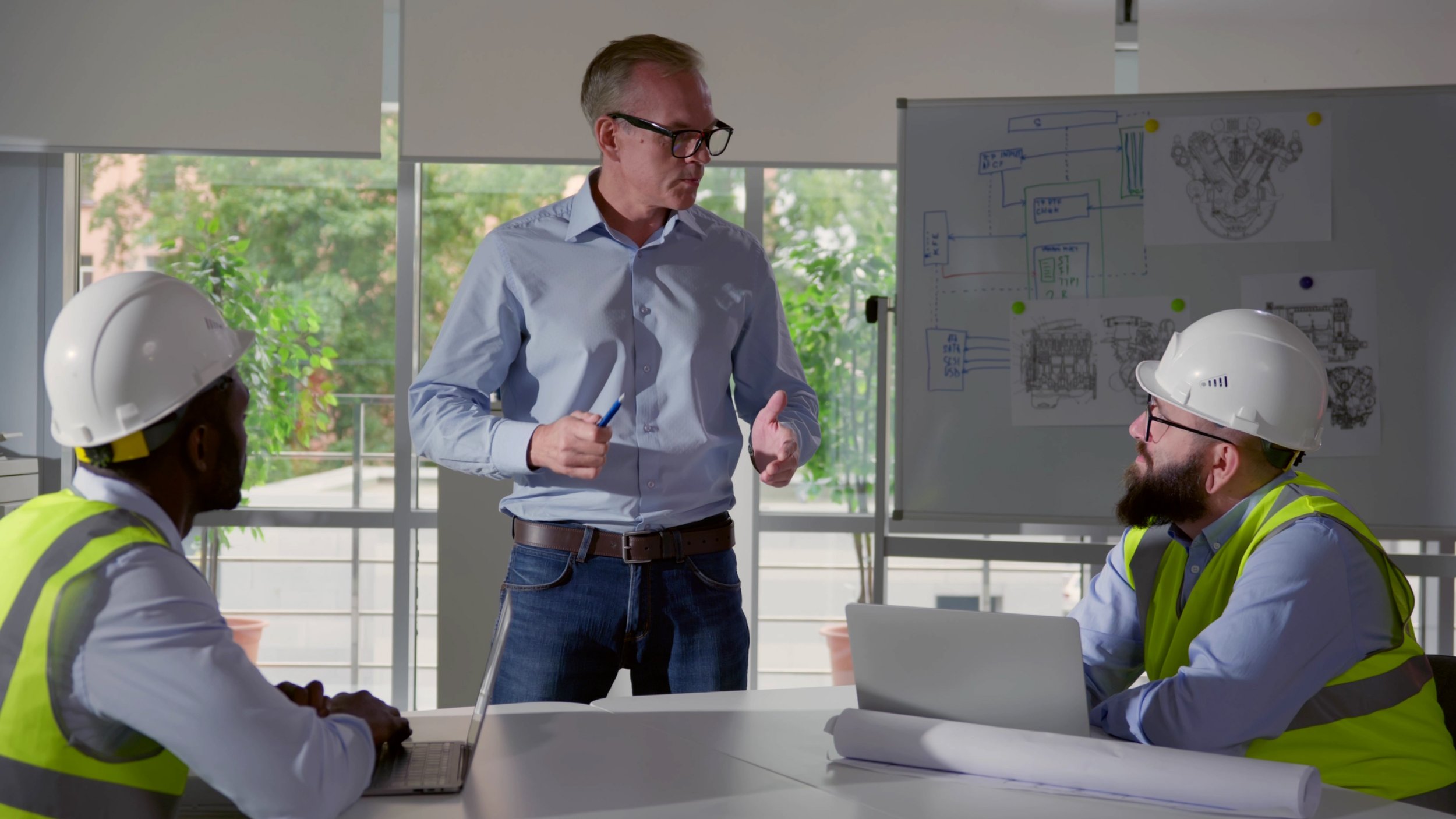